How single-use separation systems are elevating sustainable biopharma
The biopharmaceutical industry is increasingly turning to single-use separation systems, such as Alfa Laval’s CultureOne separator, due to their numerous advantages. These systems offer reduced contamination risks, greater flexibility, smoother scalability from laboratory to production, and significant time savings in cleaning and validation. Additionally, single-use systems contribute to enhanced safety while lowering capital costs and minimizing water and energy usage.
DATE 2024-11-18
A major benefit of single-use systems lies in their capacity to conserve water, energy, and chemicals. Traditional separation systems require frequent cleaning and sterilization, which demand high volumes of water, harsh chemicals and energy. In contrast, single-use separators come pre-sterilized and are discarded after use, eliminating the need for resource-heavy cleaning procedures.
Additional resource savings in single-use manufacturing
With the introduction of the CultureOne separator, Alfa Laval enables biopharmaceutical companies to significantly reduce the use of depth filter systems. Roger Lundblad, a single-use expert at Alfa Laval, highlights the separator’s environmental impact. “With CultureOne, biopharmaceutical manufacturers using single-use can significantly reduce plastic waste with each batch. In some cases, the number of filters needed is reduced by up to 80%. This not only lowers costs but also dramatically decreases solid and liquid waste.”
He further explains that the amount of waste reduction depends on batch size. For instance, a typical 2000-litres batch can save more than 500 kg of solid waste per batch with CultureOne Maxi, when compared to using single-use depth filters.
By significantly reducing the amount of consumables involved in single-use biopharma processing, CultureOne greatly improves sustainability of operations, helping companies meet their environmental goals while maintaining high efficiency.
Enhanced efficiency and scalability
CultureOne centrifuges are not only more environmentally friendly but also improve operational efficiency compared to depth filters systems. The Alfa Laval single-use centrifuges are designed to maximize product recovery, which means that more of the valuable product is captured during the separation process, with less going to be wasted. This reduces the need for additional filtration steps, saving both time and resources.
In biomanufacturing, efficiency gains directly impact both production volume and cost savings. Consider a production process using a 2000-liter bioreactor at a cell density of 10% packed cell volume (PCV), with around 1800 litres of product. CultureOne technology increases yields from 92.5% to 98%—an extra 5.5% recovery compared to traditional processes that use filters. This translates to a recovery of 99 additional litres of centrate. At a typical titer of 3 grams per liter, this results in 297 more grams of product recovered.
In the context of monoclonal antibody (mAb) dosage, this added yield is significant. For instance, with an average therapeutic dose of 5 mg per kilogram of body weight for a 70 kg patient, this enhanced productivity can support an additional 850 doses. Financially, this improvement represents a value of $148,500 over conventional single-use (SU) depth filters. Beyond the financial benefits, additional product recovery from the same inputs results in greater patient availability for treatments. The shift to CultureOne Maxi also reduces waste, making it a highly efficient solution in bioproduction.
Moreover, single-use systems like CultureOne are scalable, which is crucial as the demand for biopharmaceutical products continues to grow. Whether a company is producing small batches or large volumes, single-use systems can be easily scaled up without a significant increase in their environmental footprint. This scalability ensures that even as production increases, the environmental impact remains minimized.
Practical convenience
In addition to being resource-efficient, single-use systems are also convenient for operators. Traditional filtration systems often require extensive maintenance, including disassembly, cleaning, and reassembly that can lead to significant downtime. Single-use systems, however, come pre-assembled and ready to use. This reduces the time needed for setup and maintenance, allowing for quicker turnaround times between production runs.
As Roger Lundblad notes, “Our customers are looking for technology that not only supports sustainability but also streamlines their operations. CultureOne offers both—it’s a solution that meets the demands of modern biopharma manufacturing.”
In conclusion, single-use separation systems like Alfa Laval’s CultureOne represent a major step forward in making biopharmaceutical manufacturing more sustainable. By reducing resource consumption, minimizing waste, and improving operational efficiency, these systems offer a viable solution for companies looking to reduce their environmental impact while maintaining high standards of production.
Highlighted technologies
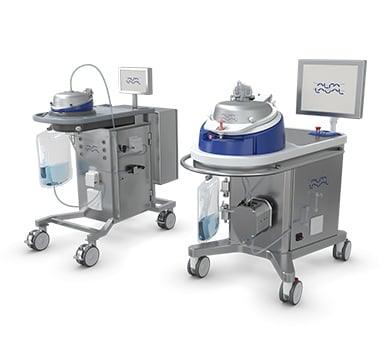
CultureOne™
CultureOne™ is a separator range designed for single-use biopharma processes. The centrifugal disc stack technology offers gentle product treatment, increased yield, and unmatched separation efficiency for high-density cell cultures.