Meeting environmental goals in the oil refining industry
Despite being in the business of processing crude oil, Chinese firm Hengli have ambitious environmental targets. Their partnership with Alfa Laval is crucial to enabling them.
DATE 2024-09-25 AUTHOR David Landes PHOTO Hengli/Pengwei sun
In less than a quarter of a century, China’s Hengli Group has grown from a single textile factory into a petrochemical giant with more than 80,000 employees and revenues of €48 billion.
In early 2019, the group reached another milestone when crude oil started flowing into a new €9.8 billion oil refinery located on Changxing Island, 120 kilometres northwest of Dalian Port on the northeast coast of China.
With a refining capacity of 400,000 barrels of crude oil per day, the sprawling facility makes Hengli one of China’s largest oil refiners.
Gazing out over the jungle of towers and tanks on the island where Hengli has had operations since 2012, it’s easy to miss that the company is considered an environmental role model.
Our goal is to maintain standards higher than the environmental protection regulations of the Chinese government. We strive to do better. We want to develop and grow in a sustainable manner.
Yanzhi Wu, Hengli’s Purchasing Division Manager
Despite its rapid growth, Hengli remains dedicated to maintaining high environmental standards, making huge investments to reduce energy use and emissions in an admittedly resource-intensive sector.
Changxing Island features an innovative embedded wastewater treatment system recognized by the International Water Association for its environmental benefits. Hengli has also participated in United Nations-organised trainings to help improve sustainability in China’s textile industry.
Alfa Laval’s role in supporting sustainable refineries
Ever since 2003, when Hengli first installed Alfa Laval heat exchangers in its production facility, Alfa Laval has been a trusted partner in helping Hengli achieve its sustainability ambitions.
“We have a fruitful relationship and our cooperation is ongoing,” adds Wu. “Alfa Laval’s equipment will always be a part of Hengli’s development.”
Belinda Lau, Alfa Laval China’s Business Unit Manager for heat exchangers in Process Industry, Energy Division explains: “Hengli is a company that wants to be at the forefront of what they do. They invest in the latest technology and want to protect the environment.”
“This aligns well with Alfa Laval and our desire to play an important role for customers in meeting their own sustainability targets.”
A 24-year veteran of Alfa Laval, Lau has been working with Hengli since the first plant project and has witnessed the evolution of the Alfa Laval-Hengli partnership first-hand.
Belinda Lau
"We built up a lot of trust over the years. It’s a very long-term process. They have confidence in our product quality and design knowledge. But it’s not all about the product itself. It’s also how we adapt the design and configuration to meet the process conditions for a particular application." Belinda Lau, Alfa Laval China’s Business Unit Manager for heat exchangers in Process Industry
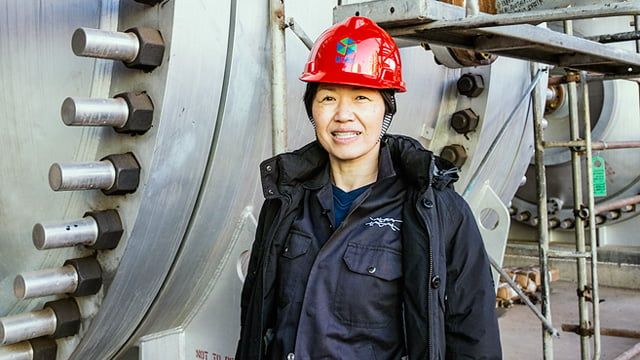
With energy costs accounting for about 30 percent of the refinery’s overall operating costs, measures that reduce energy expenditures can have a huge effect on profitability. No less important are the potential reductions in CO2 emissions due to lower fuel needs.
Alfa Laval therefore suggested Hengli install welded plate heat exchangers, which are more compact and efficient than traditional shell and tube exchangers. The welded plate heat exchangers made it possible for Hengli to design the refinery to use different process streams to preheat the incoming crude to the highest possible temperature before entering the distillation process in a very compact space. ‘’Using the process streams to achieve the highest possible temperature means crude is heated free of charge, without fuel cost and reducing emissions,” Lau explains.
While it’s too early to calculate exactly how much Alfa Laval’s heat exchangers may reduce costs and emissions at the refinery, Hengli’s own feasibility study estimated that switching to Alfa Laval’s plate heat exchangers would cut fuel consumption at the facility by 30 percent.
The intensified cooperation between Alfa Laval and Hengli in conjunction with the refinery project exemplifies what Lau characterizes as a true “win-win partnership” whereby both companies challenge the other to think differently and do better. On the one hand, Alfa Laval has pushed Hengli to consider new heat exchangers. At the same time, Hengli has pushed Alfa Laval to offer a stronger product portfolio and provide even better service.
“We help them to meet their goals for energy efficiency and emissions, and they push us to have a stronger product portfolio and knowhow,” she explains. “It’s good for us to be working with them. It forces us both to improve.”
A Alfa Laval contribui para as Metas Globais
As Nações Unidas adotaram 17 Metas de Desenvolvimento Sustentável para 2030, conhecidas como Metas Globais, que os líderes globais se comprometeram a alcançar. Agora cabe a empresas como a nossa fazer isso acontecer.
3 steps for petrochemical customers to improve efficiency and reduce emissions
-
Find opportunities to improve heat recovery by considering high-efficiency plate type heat transfer technologies
-
Consider spiral heat exchangers to increase operational efficiency by minimizing fouling.
-
Involve vendors of high-efficiency heat exchangers before the process design is fixed to get an optimal process design.
PRODUCTS
Gasketed plate-and-frame heat exchangers
- Highest thermal efficiency and close temperature approach.
- Compact units - space saving, easy to service and maintain.
- Maximum uptime - less fouling, stress, wear and corrosion.
- Flexible - easy to adapt to changed duty requirement.
Read more about Gasketed plate-and-frame heat exchangers
Welded plate-and-block heat exchangers
The Alfa Laval Compabloc range provides compact and efficient heat transfer for a wide range of clean and dirty process duties. Full and easy cleanability on both circuits makes it the most service friendly welded heat exchanger on the market.
Read more about Welded plate-and-block heat exchangers
Welded spiral heat exchangers
- Minimal fouling, or clogging, ensures uptime.
- Easy-to-open design, ensuring low maintenance costs.
- Reduced pipework and steel structures means lower installation costs.
- Increased energy savings and reduced emissions.
- Each unit is fully customized, offering the best thermal fit for the specific duty.
Read more about Welded spiral heat exchangers
Packinox
- Lower OPEX – Leads to substantial energy savings.
- Lower CAPEX – A single Packinox can replace several large shell-and-tubes.
- Higher process yield.
- Reliable, proven technology.
- Real-time monitoring and continuous optimization by Alfa Laval experts.
Are you curious?
At Alfa Laval, we always go that extra mile to overcome the toughest challenges. Our driving force is to accelerate success for our customers, people and planet. You can only do that by having dedicated people with a curious mind. Curiosity is the spark behind great ideas. And great ideas drive progress.
In our Career section you find opportunities for curious minds to have a lasting impact on some of the planet’s most urgent problems.
Advancing better. With Alfa Laval.
Our award-winning magazine
Innovative food processing to turn bugs to burgers, or new technology to store renewable energy are only two examples of articles in the new edition of HERE magazine. The articles illustrate what we mean by responsible growth, providing solutions that benefit both people and planet. HERE won the Swedish Publishing Prize in 2019.
Alfa Laval Annual & Sustainability Report
In our latest annual report, you can read about the year that past, the trends that drive our business and the industries we serve. It will also give you a better understanding of our people, products and services, and how innovation and sustainability is an important part of everything we do.
The Sustainability Report is integrated in our Annual Report.
Tags
Tudo